One of the major contributors to abnormal and erratic fuel trims, I believe, is Mass Air Flow (MAF) Sensor placement!
So let's have a look at this interesting topic!
There are four places you could possibly put the MAF Sensor when you add a turbo to your monster. This may be altered depending on the position of the blow-off valve as you could possibly place the blow-off valve before the intercooler, but the relative positions of the MAF should be the same.
1. Before Turbo:
This is actually a problem. When you accelerate and build boost, then go to switch gears, the throttle snaps shut and pressurised air gets expelled through the blow-off valve, BUT... The turbo is still spooling and is still actually drawing air through the MAF and hence it's possible that you will get a rich condition just before or when you get back on the throttle. You'll also get skewed MAF readings especially when you are decelerating with partial throttle (e.g. going down a hill). Although you are only touching the throttle, the turbo is spooling more and drawing in far more air than normal operations but all the factory computer sees is that more air is being drawn in so it will add more fuel. However, the O2 sensor will be reading rich, so this then leads to excessive fuel trimming and it is not uncommon to see -15 to even -20 STFT. This leads to abnormal behaviour in those RPM ranges.
2. After Turbo, Before Intercooler :
Again this placement is not ideal. It is still in the same airflow as under the same conditions with the MAF before the turbo, the turbo will still be pushing air through the MAF resulting in metering (measuring) airflow that may or may not eventually be used in the motor.
3. After Intercooler, Before BOV:
Again, it is not certain that the metered air that blows through the MAF will eventually be used in the motor as it could be by-passed by the blow-off valve.
4. After BOV, Before Motor:
This is the optimum placement. With the MAF in this position air that will indeed end up being used in the motor will be metered accordingly. When you are at partial throttle, the turbo and draw as much air as it wants but the actual amount of air that goes to the motor will be predicable. Even in the blow-off condition, when boost is built and by-passed, there wouldn't be any airflow to the MAF which is logical and is expected by the factory computer. The only challenge here is that the MAF will be in a region of pressurised air rather than just 'drawn in' air. Largely dependent on air temperature, you'll need to look at your tune to see if you need to adjust your stock MAF levels.
The main factors that drive the positioning of the MAF Sensor includes:
- Physical space: perhaps there is not enough room?
- Cable length: perhaps there's not enough cable length to move the MAF sensor?
So how can we avoid funky fuel trims due to MAF sensor placement?
At this present time, the most cost-effective method that retains the most amount of hair folicles on your head is to move the MAF to the appropriate position (After BOV, Before Motor). This may mean re-positioning and fabricating piping as well as rewiring to accomodate the MAF sensor.
The not so cost-effective method that may change you from being Zack Fair to Rude (refer Final Fantasy VII) is through intervention tuning by re-mapping the MAF sensor and compile a whole new MAF map.
Instead of taking in a MAF value from the sensor and adjusting it by a percentage and pushing that to the factory computer, you basically remap the entire map and for every sensor value you allocate a completely different sensor value. So for each breakpoint in the MAF map you specifically define a sensor value and regardless of what the MAF sensor sends to the piggy back, you output the value in the corresponding cell dependent on RPM and load (i.e. MAP). This is no easy feat. It maybe do-able but you'll need to get a log of all MAF values throughout the entire RPM range in a range of scenarios (idle, acceleration, deceleration, cruising etc) then extrapolate those values and add 'fudge' factors to account for the turbo. To add to the complexity, one thing that you don't have control of is intake air temperature which is sensed by the MAF sensor and is used by the factory computer to further 'fudge' the numbers to account for fluctuations. This may then necessitate two MAF maps (you can switch between two tunes on the AEM FIC by the way), one for hot days and one for cold days. As you can see, the complexity of doing this rises exponentially and the MAF map that you develope will never by ideal and you'll be tuning for weeks... months... years......
There's probably a couple of other ways to some how switch the MAF sensor signal to a single output during partial or off throttle but again, it's too complex and time consuming to consider. It would probably be easier and less stressful to just live with it and just understand what not to do to prevent fuel trims going crazy.
Tips on living with MAF induced fuel trim problems:
- Have a scan tool that reads and ouptuts LTFTs and STFTs! See when this happens and adjust your driving style.
- When you are going downhill, avoid having your foot on the accelerator too much. Again, watch your trims! If it starts going crazy negative STFTs, take your foot off for a bit and resume when trims stabilise.
- Have a scan tool that reads and outputs LTFTs and STFTs, what? Did I say that already? This will become (if not already) a permanent feature on your dash.
Good luck!
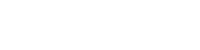
Tks for your help. Just one question, when I running and release the throttle, the A/F ratio goes to very rich, smoking a little some times.. do you have idea how to solve that ? It´s a MX3 V6 with turbo, stock ECU and stock VAF sensor.
ReplyDeleteHey Anderson!
DeleteSo if you're cruising or accelerating and you slightly let off the throttle (partial throttle), a rich condition could occur if your MAF sensor is BEFORE your blow-off valve. What is happening is that although you have let off the accelerator, the turbo is still pulling in air and the airflow is getting measured by the MAF sensor (metered). Your ECU thinks air is still going into the motor so it injects more fuel to maintain the perceived A/F ratio; leading to a rich condition. Very tricky to fix as I mentioned in my post above! The best way is to move your MAF sensor AFTER the blow-off valve.
Now if you're cruising or accelerating and suddenly let off the accelerator completely, the throttle closes and no more air can enter the motor. Again, in this siutation, if the MAF sensor is BEFORE the blow-off valve, the turbo is still drawing in air and the air is getting metered.
It's a really tricky problem as I described above... You could try to tune it out so using the MAF sensor as the load, but doing this won't give you good resolution or flexibility for tuning.
Have a go at moving the MAF sensor AFTER your blow-off valve. That should give you more accurate airflow readings.
If you MAF sensor is AFTER your blow-off valve, check your tune. Check the atmospheric pressure level or below (vacuum) break-points; if you're adding fuel here, make sure it's not excessive. If you are in vacuum, in most cases, you shouldn't need to richen your fuel delivery anyway, but assess it based on your setup and conditions!
Good luck!
Surely can't you just change your blow off valve for a recirculating valve then you won't loose the metered air that's throwing out your fuel trims
ReplyDeleteHeya Adam!
DeleteExcellent point!! Plumbing back the air will prevent it being lost.
Though consider the scenario with the MAF sensor placed before the turbo. When the throttle shuts closed, air is still being drawn by the turbo even through a recirculating by-pass valve, leading to the rich condition. The position of the by-pass plumb back before or after the MAF sensor also needs to be considered. If the MAF sensor is not placed between the motor and by-pass valve, although the metered air is recirculated, the MAF sensor will still read the air flowing through the system, not air that is actually being consumed by the motor. This is the predicament of the MAF sensor and hence why manufacturers have moved towards Manifold Air Pressure (MAP) sensors.
If however anyone happens to observe the correction of the rich condition through the implementation of a recirculating by-pass valve, please let us know! Understanding how it works will be very useful!!
is it possible to remove the maf and just clamp very early and use the map sensor in vac and boost?
ReplyDeleteHolla! Thanks for visiting and good question! If you can simulate a MAF signal through the MAP signal then possibly.. but this is really difficult because they measure different things and do not have a linear relationship.
DeleteThe factory ECU will be expecting an MAF signal so you’ll need to somehow provide it. You can clamp it when in boost to give you a sorta fixed signal for tuning. But the main issue is when you’re in vacuum. There isn’t that linear relationship between air pressure (MAP) and air flow (MAF), sure, as RPM rises, flow and pressure rise but not at the same rate and not at the same values. Plus add in the error rate of hot wire MAF and pressure signal and now you’ve got one complex translation to make.
The best you could do is spoof the MAF signal, loosely based on MAP. It requires a fair bit of trial and error to tune your spoofed signals and after all of that, it might just be easier to just keep the MAF sensor for vacuum tuning.
If you really don’t want your MAF sensor or if placement is difficult, you can always give it a go. Just make your spoofed values slightly conservative and aim for a slightly rich O2 measurement at the other end to safe guard against knock and pinging.
Let us know how you go!!
All the very best!
Hi,
ReplyDeleteGood article and some interesting info and helped me with some of the mods I have been doing on my (Alfa Romeo) Turbo Diesel Engine. The first mod I had carried out was to change out the original airfilter housing and tubing and go for a simpler filter and cold air induction set up, which worked quite well. This however kept the MAF before the turbo. I then changed the old turbo hoses to a combination of silicone joints and hard tubes, mainly ‘cause the old hoses were going soft and you could see them expand!
I did ponder at times if there was a better position for the MAF as there had been chat on an AR site that if the MAF was too close to the turbo it could cause problems. This made me do a google search and I found your article and info. I got a new MAF with a bigger housing and modified the top hose to suit the new setup. So the MAF now sits straight after the Intercooler as I think the intercooler will help steady out the air flow. I really only finished this today and the car started and idled fine, I took it for a quick test run and she actually feels a bit smoother and the acceleration from 50mph + feels way better. I haven’t had a chance to scan the ecu to get readings from the maf and other sensors and I have left the original maf in position so I can compare the values when I get a chance.
I have read a few other articles and they have thrown up some questions about this placement. Primarily about oil mist having a detrimental effect on the MAF operation and the variation in boost causing variations in air temp that may affect the MAF values sent the ecu?
Have you come across any of the issues and have any advice? Im going to monitor this for a while and see how the car runs over the coming weeks and hopefully get some data too.
Cheers,
Alasdair
Hi there! Thanks for visiting! From how MAF meters work, I believe the position I described is probably the most optimal but I’d be totally happy to be proven wrong!
DeleteWith regards to oil mist, you’ll get this issue if you plumb back your crank case breather line anywhere before your MAF. You can either move the breather line after the MAF so any oily air can “skip” the MAF or, use an oil catch for all your crank/motor breather tubes. Usually good practice anyway, just as long it’s a closed loop breather system so you don’t affect emissions!
Let us know how you go! All the very best!!